If you’re looking for the perfect excuse to buy that big, beautiful Bridgeport mill, we’ve got some bad news: it’s not going to be making perfectly square end cuts on aluminum extrusion. Sadly, it’s much more cost-effective to build this DIY squaring jig, and search for your tool justification elsewhere.
There’s no doubting the utility of aluminum extrusion in both prototyping and production builds, nor that the versatile structural members often add a bit of class to projects. But without square cuts, any frames built from them can be seriously out of whack, leading to misery and frustration down the road. [Midwest Cyberpunk]’s mill-less solution uses a cheap Harbor Freight router as a spindle for a carbide endmill, riding on a laser-cut acrylic baseplate fitted with wheels that ride in the V-groove of — you guessed it — aluminum extrusions. A fence and clamping system holds the extrusion firmly, and once trammed in, the jig quickly and easily squares extrusions that have been rough cut with a miter saw, angle grinder, or even a hacksaw. Check out the video below for a peek at the build details. Drip Edge Roll Former
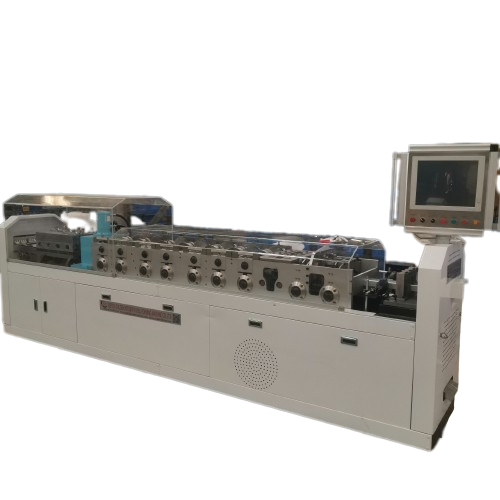
We love the simplicity and utility of this jig, but can see a couple of areas for improvement. Adding some quick-throw toggle clamps would be a nice touch, as would extending the MDF bed and fence a bit for longer cuts. But even as it is, this tool gets the job done, and doesn’t break the bank like a mill purchase might. Still, if your heart is set on a mill, who are we to stand in the way?
Apropos of nothing, why won’t my bridgeport mill make square end cuts in aluminum extrusion?
I didn’t view the full video – is that explained somewhere? I’d really like to know the explanation behind the statement.
He didn’t say his mill didn’t cut square – he said he didn’t buy a mill because it wouldn’t have been right for his workspace or wallet. He did say that he wasn’t able to get properly square cuts from his miter say.
That matches my experience, miter saw blades will have some deflection. Even my fancy DeWalt miter saw with the nicest, thickest carbide tooth blade has had problems not deflecting when trying to square up an existing cut.
I also like that this can be used to cut slots or other shapes!
mmao88 , This has been my experience. I use a new TCG blade for aluminum and it does a great job for “rough” cuts but the deflection causes a kerf of .1mm or more every time. I can see why people don’t care because the kerf is negligible to them or maybe they’ve found a saw that can do perfect 90 degree cuts (if those exist?) but the imperfections from my craftsman miter bothered me and this was a fun project.
What is the rake angle? I have done well with a triple chip carbide with zero deg rake angle and cut lots of 1/4 inch aluminum plate and rods and such.
https://www.amazon.com/gp/product/B01LXDARMZ/ref=ppx_yo_dt_b_search_asin_title?ie=UTF8&th=1 I think 0 degree or no rake angle
I used to use a 14″ TCT circular blade at about 18000 RPM. The Centrifugal force at that RPM is probably just below tensile strength and kept the blade perfectly straight. I used wax (paraffin) and never placed any part of my body inline with the blade! but yeah perfect cuts every time.
PS: Don’t try this unless you know how to calculate blood loss in litres per nano-second if the blade shatters.
There are robust miter saws for metal taht do a rather good job. But generally used more generic ones for the last decade or so.
How precise are is the square required to be? With technique, miter saws can be pretty good. Not a mill, but ever so close.
“it’s not going to be making perfectly square end cuts on aluminum extrusion”
That’s exactly what he said.
“It” here is “a perfect excuse to buy a Bridgeport mill”, not “a Bridgeport mill.”
Drop quotes around “making perfectly square end cuts on aluminum extrusion” and it reads a lot clearer. In conversation it’d be a lot clearer (you’d just pause after “be”).
Though if you’ve got a dozen poor excuses for getting one, you might be in better shape than the dude with a 30% single excuse, cost/benefit wise.
I think it’s saying, you don’t have an excuse to buy it just for that, because here’s a cheap/good way to do it, not that it can’t do it.
Right…should read more like: “If you’re looking for the perfect excuse to buy that big, beautiful Bridgeport mill, we’ve got some bad news: that excuse is not in order to make perfectly square end cuts on aluminum extrusion.”
Though it’s got 2 axes and a spindle so coulda said, don’t buy a fullass mill when you can build a halfass mill. :-D
I wrote an almost identical reply, before realizing, after a bunch of re-reads, that it’s just poor wording…
Before folks chime in with “why not just use a miter saw or chop saw,” remember that blade deflection is always present, they won’t get as easily repeatable cuts. This is also better for truing existing faces — if you had a piece that was cut at 89 degrees you’ll have a hard time getting the saw blade to not deflect against the shallow angle.
This type of jig could also be used to cut vertical slots or other shapes that a saw most certainly can’t do.
Because router spindles are perfectly concentric and don’t deflect? Plexiglass plates and rubber wheels have infinite modulus of elasticity?
Your not wrong, but stopped halfway.
Especially a “Drill Master” brand router from Harbor Freight!
The idea is sound, it needs to be re-worked with less potentially squishy things in it.
Jimmy Dubs – I get drill master isn’t a reputable brand but this router is an exception. I will actually measure the runout but the results in the video speak for themselves. I tested with several feeler gauges and couldn’t get one under the square. I later used a real machinist’s square, and it was the same result.
Endmills bend, even thick endmills. Ringless engine designs count on this deflection to make pistons seal at the top of the stroke.
The fact you haven’t been able to measure the runout says more about your measuring than anything else. Don’t use sparkplug gap setting feeler gauges.
Being able to see light through the gap is about 1/10 of a thou (units just to annoy the SI dweebs). Set the square and the extrusion on your surface granite, don’t preload and line them up with some bright sunlight.
Your eye is likely the squarest and straightest tool in your box. Not mine though, but it’s still close.
Doesn’t bother us SI Dweebs, it’s just – “about” 0.000254mm sounds a bit odd.
That looks to be a substantially larger footprint than some mini-mill, which will come with advantages of considerably better motor and gearbox, the ability to fit a wider range of tools, more control of cut depths and lengths – its just a more versatile tool.
This is certainly a perfectly good jig to throw up with parts you have and maybe you can store it more easily, nothing against it at all as a tool, when even the flexibility of these extrusions looks rather well dealt with how can there be really. But don’t rule out getting a small mill into your space, they are surprisingly capable really, if often way more challenging to sort out work holding than the big iron, could certainly handle this job trivially if you had one.
It could be his butter bot “What is my purpose?” “You cut square edges” i.e. he wants to leave it jigged up like that ready to go because he frequently cuts square ends and doesn’t want to re-jig a multipurpose tool every damn time.
Very possible and another perfectly valid reason, my only point was don’t rule out the baby sized mills as pointless, they fit in tiny spaces and can do useful work.
Begs the question, what does he use to cut the extrusions in the first place?
As one of the youtube comments says, “A lot of work to replace a chop saw.”
If your design is relying on the ends being square to a tenth of a millimeter, you’re doing something wrong or silly.
For example, making a square bracket without cross-braces or corner braces, relying only on the ends of the bars to make it square.
>> If your design is relying on the ends being square to a tenth of a millimeter, you’re doing something wrong or silly.
Voron Design has entered the chat.
>> For example, making a square bracket without cross-braces or corner braces, relying only on the ends of the bars to make it square.
Exactly how Voron 3D printers are designed – butted joints. Mind you, the official spec states you should order pre-cut genuine Misumi profiles, and a single set of those will cost €/$ 150-200. So it may be worth making such a jig if you have the parts lying around and prefer cheap no-name alu profile, or you want to become a supplier of Voron parts. But arguably, if you are spending $1500-2000 on a DIY 3D printer, then faffing about for half a day or more building, calibrating and testing this jig in order to save $50-100 on alu profile for a single printer is rather thin gruel.
Not gauge blocks, not the instruments at CERN, not at NASA, not your super square HS coach.
Perfect doesn’t exist. There are no perfect square cuts in existence, anywhere. Closest you can get is likely a cleaved crystal.
Bet my bandsaw gets closer to perfect square then this contraption, if I took the setup time. Granting it’s big. No way this thing is as close to square and straight as a decent Bridgeport.
Attempting to get to perfect is a quick way to go broke or get smart.
Pretty sure a Bridgeport mill can cut square enough end cuts on aluminum extrusions.
Define ‘square enough’, tell me about the Bridgeport’s history, how the extrusion is held and the cutter used.
I could easily screw it up. Length of exposed extrusion tuned to so resonant frequency is the same as spindle RPM * cutter flute count.
I’ve seen a beancounter step out of her space and add a zero to a drawing. She wouldn’t let me add a zero to my check, didn’t get how the two were related, her zero was to the right of the decimal. Still don’t know what she was thinking.
Still leaves sharp edges. Just more square and shorter sharp edges. Needs to build something that can quickly sand or file the ends as well because doing so manually takes far longer than it should!
Get an adhesive backed sanding disc, at 220 grit, and stick it on a piece of scrap plywood that’s >= 0.375 inch thick. Trim and round off the edges leaving 0.25 inch around edge of sandpaper.
Leave your new sanding block within reach of your cutoff saw.
After cutting off some material, scuff the newly cut edges with your sanding block. Gloves are recommended but not required as you’ll be holding the block instead of a file and making short scrubbing motions – pushing away from you.
Did Aluminum Extrusion get more expensive too, or does someone have a good cheap source for it?
The price of Aluminum is especially volatile at the moment, so that’s probably being reflected in extrusion prices too. Some brewers are stocking up on cans because they are concerned about availability over the next few months…
I’d have thought they would stockup on can ‘coins’. The things that are hammered into cans.
As opposed to where they get hammered out of cans, probably Tennents extra in Scotland and VB in Aus.
I think if he used a higher quality chop saw and /or a higher quality blade – he wouldn’t be using a fancy jig to re-cut the extrusion. My 12in Dewalt miter saw will cut aluminum extrusion fairly perfectly. I quick sand with the orbital sander – and you can have a super smooth edge on it as well if you need it.
I agree – my cold cut saw does a pretty good job of square cuts in steel, let alone aluminum, and they are not expensive or that hard to put somewhere..
However, I do have a jig for big square cuts of wood panel…
Squaring extrusion is a very poor excuse to buy a mill…. Much better to buy a nice lathe with a big spindle bore.
We use extruded aluminum for making work benches all the time and just use a chop saw to cut it. Pretty square!
Over the past few decades, I’ve used several miles of 80/20 extrusion for prototyping manufacturing systems ( robotics ) at GE and Boeing.. We just used a chop saw. Put the precision where you need it.
A router on a frame… kind of is a mill, without the fancy axis control.
Interesting approach – and it has given me an idea for making a trenching jig for my woodworking router. However, I cut Al plate and heatsink extrusions with my Makita mitre saw. There are a couple of challenges – fthe first is clamping the material so it is square and does not move and the second is dealing with all the chips – they get everywhere & here in the UK the weather often precludes working outdoors!
I know what it’s like, use what you’ve got. And why cut aluminum when you can build a jig, or better, a machine. This does look like a job for one of those horizontal bandsaws though. The cut quietly, straightly, and very independently. I just love sitting down with a cup of tea and watching the machine work.
Wouldn’t it be just easier and a lot more versatile to use a router table with a carefuly squared up sled ? Looks like a very expensive for a single use…
Golden rule of jig-making: If you ever have to make more than three of something, build a jig to do it. The router can be taken off of this and the thing hung up on the wall until needed again. Of course some sort of jig for your router table IF YOUR HAVE ONE will do just as well.
Well with a router table you wouldn’t even need a jig… Set up the fence just shy of the bit, put the extrusion against the sled and fence, push, done… Not saying he shouldn’t have built a jig, just saying a standard router table would probably have been a lot more useful and versatile for the same kind of money/effort, while also fullfiling the exact same purpose Also, making a table/sled setup rigid and precise may be easier than the whole plate/rollers assembly
amen. I got a really good deal on a bunch of 4545 (and other) extrusion so I’m building a lot of stuff with it (because I can) so it will for sure be worth it. The cutter itself was one of these “because I can” projects. I’m not sure why people are having so much trouble with that lol…. Yeah, a mill would be better. Yeah a miter saw can do an ok job. There are a lot of different ways to cut extrusion, but this is hackaday and this is my hack for getting almost mill like results for a fraction of the cost.
This is HaD, we’ve got a lot of people who don’t have anything better to do.
Heh. The rule is, you share something cool you are proud of and we pick it apart or tell you why it’s the wrong answer, isn’t it? Thanks for playing lol. I think it’s a cool hack.
Please be kind and respectful to help make the comments section excellent. (Comment Policy)
This site uses Akismet to reduce spam. Learn how your comment data is processed.
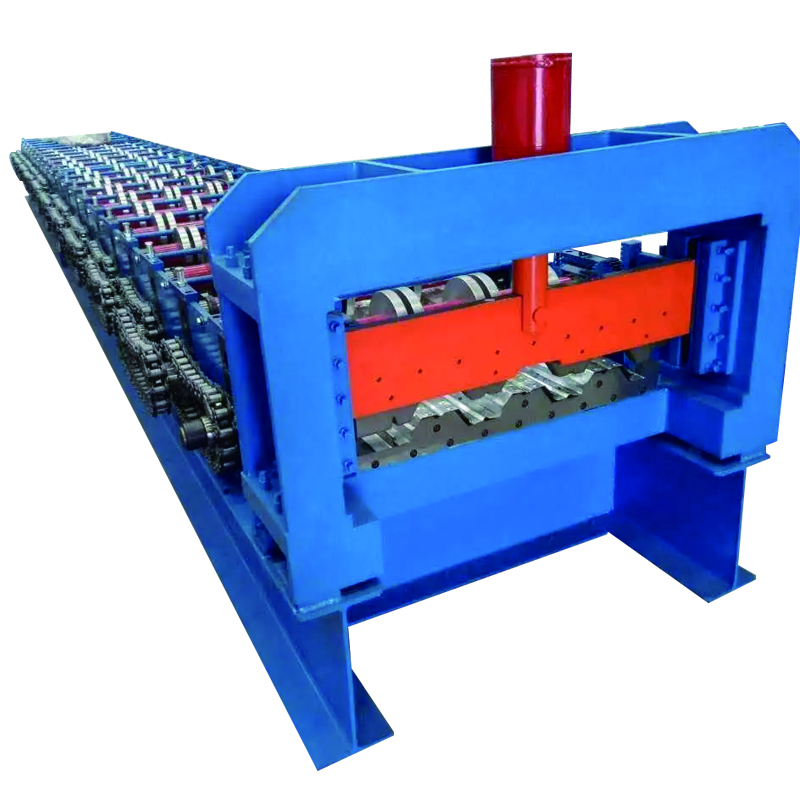
Sheet Coil Cutting Machine By using our website and services, you expressly agree to the placement of our performance, functionality and advertising cookies. Learn more